These cookies make our website work. They include logging personal details, like login/sign-up or account data, browser information, images & videos, and shopping cart journey.
In addition, we use optimization cookies to test new features and designs on our website. The information collected helps us improve our website and customers' experience.
These cookies are used to understand the performance and relevancy of our adverts, to provide you with personalised adverts on other websites and social media, to track when you have arrived at our site from a recognised third-party affiliate website, and to track if you made a purchase based on the adverts we displayed to you.
These cookies enable us to provide personalised product and content recommendations, to make the browsing experience more relevant to you.
These cookies are used to offer customer surveys and feedback, to improve search results, and to allow you to share content from our website on social media.
These cookies help us improve our website by collecting and reporting information on how you use it.
CDI CONTROL DEVICES
Since 1963, Control Devices Inc. (CDI) has been manufacturing high-quality valves for air compressors, automotive & water treatment systems and pressure washers. The company is headquartered in Missouri, USA. Read More
Filter
Pneumatics
Plumbing
HVAC and Refrigeration
Outdoor Equipment
Pneumatics Filter
Pneumatic System ComponentsView all
Pneumatic Check Valves Cast-brass valves used to allow air to flow through air compressor only in one direction; can withstand back pressures up to 400 psi and offered in different sizes, connection types and mounting types
Pneumatic Safety Valves Pneumatically Operated Drain Valves
Air Compressor AccessoriesView all
Compressor Valves Pressure relief and pneumatic drain valves used in applications where low flow and variable pressure is required. Feature a stainless-steel poppet / fluorocarbon O-ring and have a maximum operating temperature of 250 degrees F
Engine-Driven Compressor Controls Used to reduce engine speed to zero when compressor is unloaded, thereby saving fuel, and reducing engine and compressor wear. Feature a vinyl-coated stainless-steel cable with brass cylinder and can fit engines of up to 15 hp power rating
About Cdi Control Devices
CDI's extensive product line includes the compressor, float, check & pneumatic control valves. The brand's float valves have stainless-steel rods for structural rigidity and corrosion resistance. They offer a maximum pressure of 120 psi. These valves feature brass / plastic / stainless steel / stainless steel with PTFE or Viton seal. They have NPT / FNPT / compression connections to control the flow of fluid. These NSF-compliant valves can withstand temperatures up to 550 degrees F. CDI safety valves have brass / stainless steel construction for structural rigidity and corrosion resistance. These valves feature a lead / silicon rubber seals to prevent leakages and can operate at temperatures up to 250 degrees F. They come with a stainless steel / zinc plated music wire spring for increased durability and improved performance.

Things to Consider

Cross-Reference Alternatives
Some CDI MPNs cross individual references to the equivalent Honeywell model numbers. So, if you're looking for a competitor item that is either out of stock or obsolete, chances are Raptor Supplies has the equivalent CDI products available.

Shipping
These CDI products range from small to large sizes. They may require careful packaging as some items might get damaged while shipping. Hence, these CDI items are delivered by courier shipment and air freight for minimum downtime.
Major Trade Names
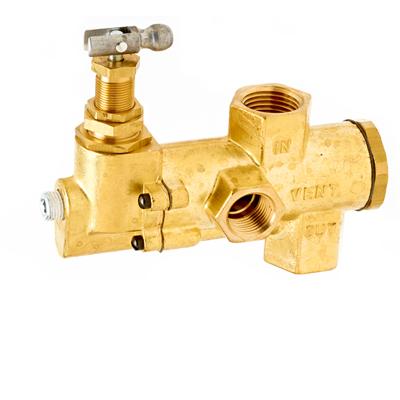
Mark Load Genie
Mark Load Genie is a pressure regulator used to maintain consistent water pressure in residential and commercial buildings. It is installed on the main water line and uses a diaphragm to control press...Read more
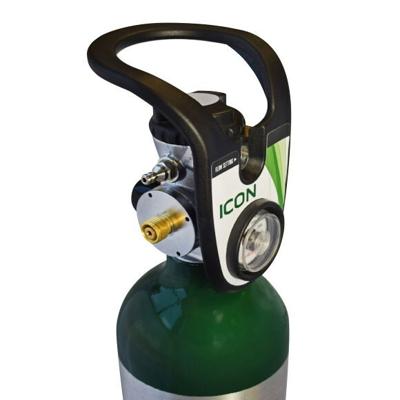
ICON Valve Integrated Pressure Regulator
ICON valve is ideal for medical clients by streamlining oxygen delivery to patients, eliminating the need for separate oxygen cylinders and regulators across their facilities. With the ICON valve, med...Read more
Frequently Asked Questions
What is the difference between safety valves and relief valves?
Safety valves are spring-loaded and open fully at a set pressure to release excess pressure, making them ideal for systems where overpressure could be caused by a process malfunction or human error. On the other hand, relief valves open gradually and relieve pressure over a range of pressures instead of at a single set pressure. They typically use a spring-loaded or pilot-operated mechanism and are often used in systems where overpressure could be caused by thermal expansion or other slow pressure changes.
How do I choose the right float balls for my needs?
- Determine the specific application, including fluid type, temperature and pressure requirements.
- Choose the appropriate material for the float ball, such as plastics, stainless steel or brass, based on the application requirements.
- Ensure that the size and weight of the float ball match the buoyancy requirements and installation space.
- Consider any additional features, such as coatings, threads and connections, that may be necessary for your specific application.
How do I set my LGM, P25, or P25V valves to my desired pressure settings?
- Loosen the range screw jam nut
- Turn the range screw clockwise to increase the levels or counterclockwise to decrease them.
- Start the compressor and note the cut-out and cut-in pressures.
- Adjust the pressures using the range screw as needed.
- Tighten the range screw jam nut once the desired pressure levels are set.
- If a differential adjustment is necessary, adjust the cut-in pressure to the desired level using the same steps as before.
- Loosen the differential screw jam nut and turn the differential screw clockwise to raise the cut-out pressure or counterclockwise to decrease it.
- Tighten the differential screw jam nut once the desired cut-out pressure is set.
- This adjustment should not affect the cut-in pressure set in Step 4, so the adjustment is now complete.